Tunnel brings power to South East England
To facilitate high voltage power distribution in the South East of England, Morgan Est needed to build a 3.05m diameter cable tunnel to house the required heavy duty power cables. They decided to form the tunnel by boring, using the TBM method. This would necessitate the tunnel lining of the front and back shunts, which were to be 3.9m in diameter, being formed by a primary and secondary sprayed concrete lining with an effective waterproofing membrane sandwiched between two layers.
Stringent waterproofing requirements for concrete lining
The chosen waterproofing system needed to be capable of forming a tenacious bond to both layers of sprayed concrete as well as being tough enough to withstand the application of the second concrete lining.
The waterproofing system of choice required the ability to tolerate difficult site and weather conditions due to the application being done in February when the temperature was between 0oC and 4oC. These cold temperatures would have precluded the application of many systems based on other resins. The use of a liquid, sprayed system that easily followed contours of the tunnel meant that no time consuming, costly scaffolding or detailing associated with sheet membranes was necessary.
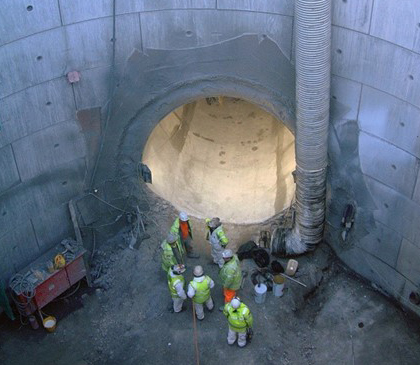
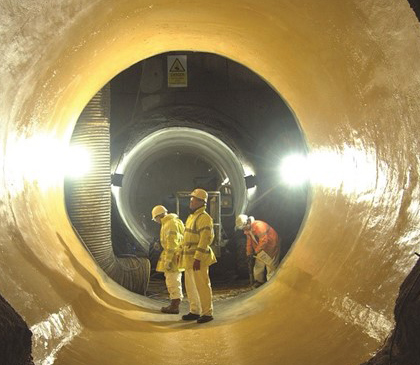
Seamless waterproofing membrane proves highly effective
The waterproofing system that met the requirements of the project was the INTEGRITANK® HF system from Stirling Lloyd (now GCP Applied Technologies). Based on unique ESSELAC® technology, this seamless, cold, spray-applied membrane holds an unparalleled track record of success. INTEGRITANK® HF provides an excellent bond to sprayed concrete and easily withstands the forces exerted by spraying concrete.
The application itself consisted of a primer to enhance the membranes bond to the substrate, followed by two colour coded coats of the INTEGRITANK® HF system. Ensuring quality control for the project was straightforward. The two colour-coded coats of waterproofing enabled fast visual inspection. In addition, wet film thickness testing ensured thickness levels and electronic ‘holiday’ testing was used to confirm the integrity of the waterproofing.
Pull off tests confirmed that the bond achieved by INTEGRITANK® HF exceeded the specified value of 0.3N/mm2. By using the INTEGRITANK® HF spray-applied system, Morgan Est produced a tunnel with not only effective, long-term protection for the valuable payload contained within, but produced it in a very cost-effective manner that decreased build time and costs.
Blue360sm Total Business Advantage.
The power of GCP products, performance and people
gcpat.ae | United Arab Emirates customer service: +971 4 5139560
GCP Applied Technologies Inc., 2325 Lakeview Parkway, Alpharetta, GA 30009, USA
P. O. Box 5006, Office 2104, 21 Floor, The Exchange Tower, Opp. JW Marriott Marquis Hotel, Business Bay, Dubai – United Arab Emirates
This document is only current as of the last updated date stated below and is valid only for use in the UAE. It is important that you always refer to the currently available information at the URL below to provide the most current product information at the time of use. Additional literature such as Contractor Manuals, Technical Bulletins, Detail Drawings and detailing recommendations and other relevant documents are also available on www.gcpat.ae. Information found on other websites must not be relied upon, as they may not be up-to-date or applicable to the conditions in your location and we do not accept any responsibility for their content. If there are any conflicts or if you need more information, please contact GCP Customer Service.
Last Updated: 2025-05-15
https://gcpat.ae/en-gb/inspiration/project-profiles/integritank-hf-system-overcomes-harsh-weather-conditions