Global carbon tax drives demand for cement grinding optimisation
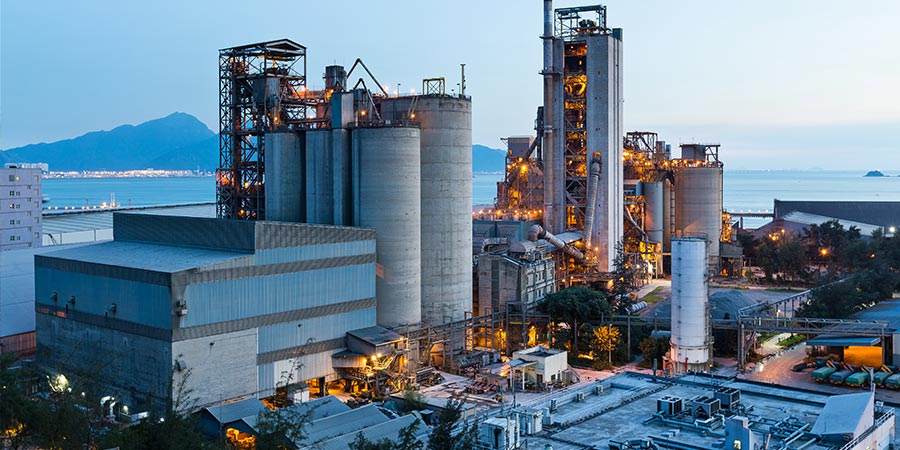
Cement is the world’s most prevalent manmade material, with some 2m3 of concrete produced for every inhabitant. With such a large volume, it is not surprising that every aspect of manufacture has potential for major impacts, both economically and environmentally.
Cement manufacture accounts for a significant part of manmade CO2 emissions, and many manufacturers have made public commitments to significantly reduce net CO2 emissions, with reduction protocols established and legislation in place worldwide, including CO2 taxes and emission trading schemes.
The majority of CO2 produced during cement manufacture arises during clinker production, due to the calcination of calcium carbonate, fossil fuel burning and electricity consumption (mostly for grinding). Using a base CO2 factor of 862kg CO2/t clinker, each one percent drop in clinker in cement can reduce emitted CO2 by 8-9kg/t cement.
Clinker in cement can be substituted to some degree with SCMs (materials such as blast furnace slag, fly ash, pozzolans and limestone). However, increasing the SCM level usually results in somewhat poorer cement strength performance. For example, although slower early-strength development is most commonly the limiting factor, each one percent increase in SCM can reduce 28-day mortar strength by some 0.2–0.8MPa, depending upon SCM type, clinker quality and cement fineness. Increasing the level of clinker replacement while still maintaining market acceptance can be significantly assisted by appropriate application of a chemical additive, such as GCP Applied Technologies’ OPTEVA™ HE quality improvers.
These are compounds that, when integrated into the cement manufacturing process, allow cement producers to increase the output and efficiency of grinding and significantly improve the performance, quality and handling of the finished cement, thereby allowing an increase in cement productivity and profitability. While the principal advantage of such additives is to create economic gain from lower cement compositional costs, increased output and increased cement volume per ton of clinker, they can also provide lower CO2 emissions per ton of cement.
The selection of the appropriate additive largely depends on how the SCM influences cement performance. For example, slag and fly ash have negative influence on early strength and setting time, so that additive formulations are used that can shorten setting time and increase early strength. Limestone cements require an additive that can increase 28-day strength. See the figure below for an illustration of how an additive can improve the strength of a limestone-blended cement.
Formulated cement additives have been used for more than 80 years, and can readily provide strength gains in the range of 2–10MPa (both early and at 28 days). Thus, it is quite common that cement additives can lower clinker factor (increasing SCM levels) by some 3-10 percent. The economic benefit arising from lower clinker factor is not discussed here, but largely depends on the cost differential between SCM and clinker. Reducing clinker factor does, however, provide a direct reduction in emissions of CO2/t of cement, by some 26-86kg, or 3-10%.
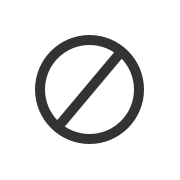