Control flow concrete for mass pours
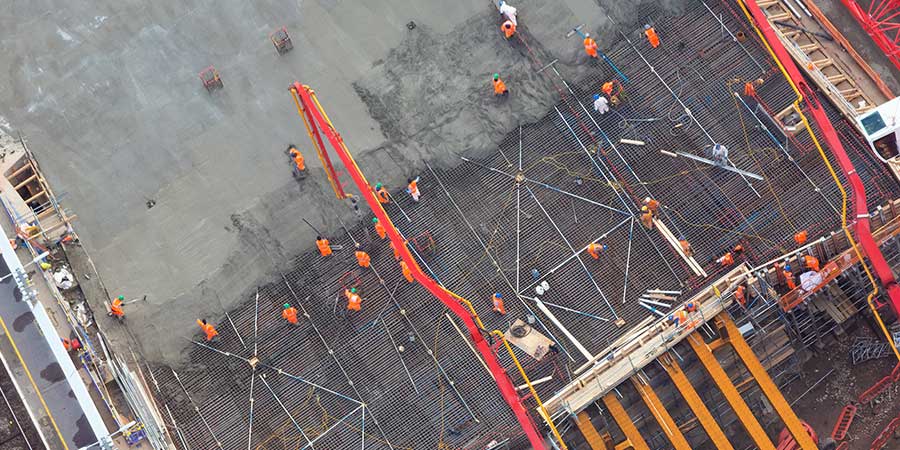
Mass pours have typically been used for foundations, columns, beams, as well as enormous structures like dams and bridges.
What are mass pours?
Many structural elements, such as shear walls and transfer girders, require large amounts of concrete. Traditionally, jobs were considered mass pours if the cross-sectional dimension of the concrete element was three feet across or more.
For these massive jobs, there is a concern both about the maximum temperature produced during concrete production and maximum temperature shifts that can occur before the concrete finishes curing. During the cement hydration process, the interior temperature of the concrete rises, while the outer concrete may be cooling. If the external and internal temperatures of the concrete differ too much, the concrete element will crack.
What is control flow concrete?
In the past, concrete contractors had two types of concrete to choose from in terms of flowability:
- Conventional concrete is relatively inexpensive, but is very labour-intensive to place and finish
- Self-compacting concrete has high flow, but is typically more expensive due to its special mix design and requires more intense jobsite quality assurance to ensure the right consistency
Control flow concrete bridges the gap between conventional and self-compacting concrete. It offers a higher flow than conventional concrete, using a conventional mix design.
Concrete Type | Conventional Concrete | Control Flow Concrete | Self-Consolidating Concrete |
---|---|---|---|
Slump or Slump Flow | 6-8” slump (150-200 mm) |
16-25” slump-flow (410-635 mm) | Greater than 25” slump flow (640 mm) |
Water-to-cement ratio | 0.42 | 0.42 | 0.40 |
How does control flow concrete help with mass pours?
- Improved concrete quality. High flowing concrete is very beneficial for mass pours. However, in the past, concrete producers needed high cement content, which would result in higher core temperatures, in order to achieve high flow. Control flow concrete alleviates this problem. It provides high flow and segregation resistance, without requiring high cement content. It is created by adding CONCERA™ admixture to a conventional mix design. Since there’s no need for high cement content to produce control flow concrete, the core temperature of the concrete will be lower. As a result, the difference between core and outer temperature of the concrete will be lower and there will be less likelihood of cracking. Less cracking will help protect against corrosion of the reinforcing steel.
- Reduced labour costs. Mass pours require tremendous resources. For example, it took 18 hours to pour the foundation for San Francisco’s largest skyscraper, the Salesforce Tower. Seven boom pumps– along with a small army of workers – moved concrete from the truck to the foundation. Control flow concrete cuts labour hours, since it’s easier to place and finish than traditional concrete. On mass pour jobs, those labour efficiencies are even greater given the number of workers typically needed for the project.
- Faster construction. Control flow concrete is extremely workable, which helps accelerate project times. There is minimal need for vibration due to the high flow, as well as its responsiveness to external energy. The concrete moves quickly in response to external energy and can also be stopped quickly when needed. In addition, the admixture extends slump flow life, which helps make placement of the concrete easier.
- More predictable results. CONCERA™ admixtures have strong water tolerance, so the concrete is less likely to have slump flow fluctuations. This helps ensure a consistent quality of concrete from batch to batch.
Learn more about CONCERA™ for control flow concrete
Tags
- CONCERA™
- Concrete
- Concrete admixtures
- Ready Mix